Technical & Services
With a steadfast commitment and relentless efforts from our entire team, Anniwan is fully dedicated to providing the highest quality services and technical support to our clients. With our profound knowledge of UV technology and over 20 years of experience in the UV industry, we assist our clients in creating new specifications, analyzing lamps with unknown data, and resolving various troubleshooting issues.
The following are our main services: – Testing for lamp data
– Analyze & develop new lamps
– Troubleshooting
– Optimize UV systems
– Electronic repair
– Supply of UV accessories
– Customer service
Testing for lamp data
At Anniwan, we have the essential equipment, power supplies, tools, and instruments needed to test any lamp submitted by our clients. Consequently, we provide our clients with accurate and comprehensive lamp data, along with professional advice to assist them in selecting the most suitable power supply and designing the best-matched UV system. As a result, our clients achieve optimal lamp performance.
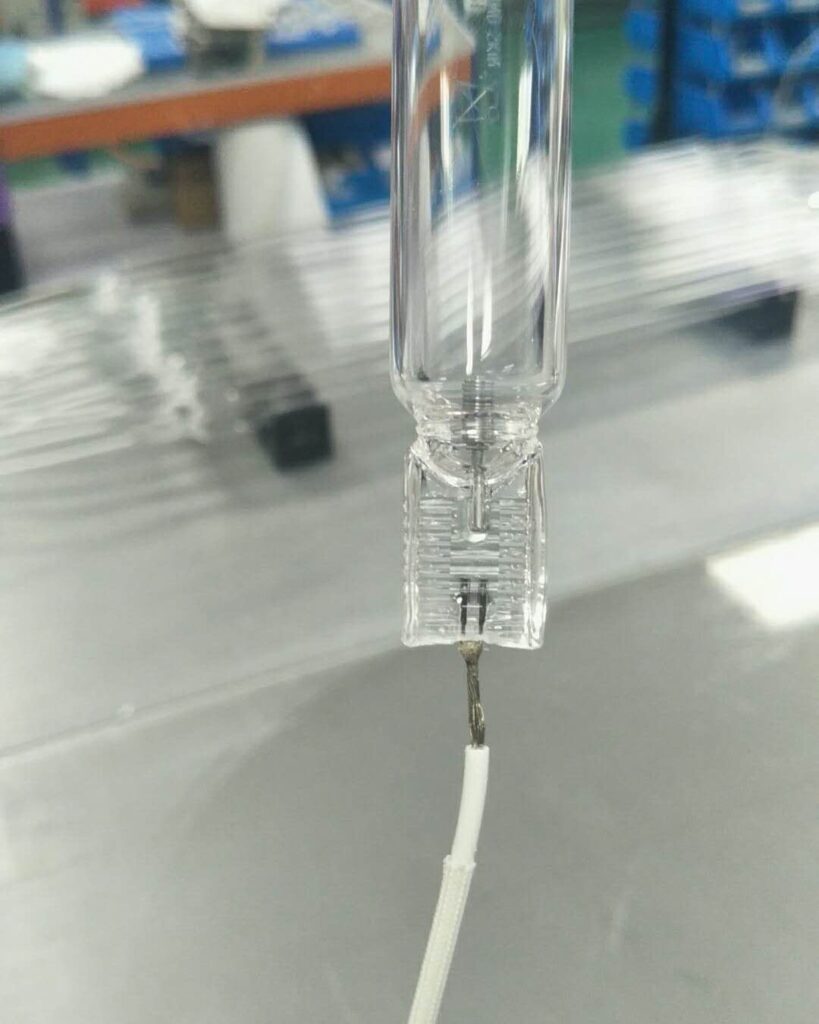
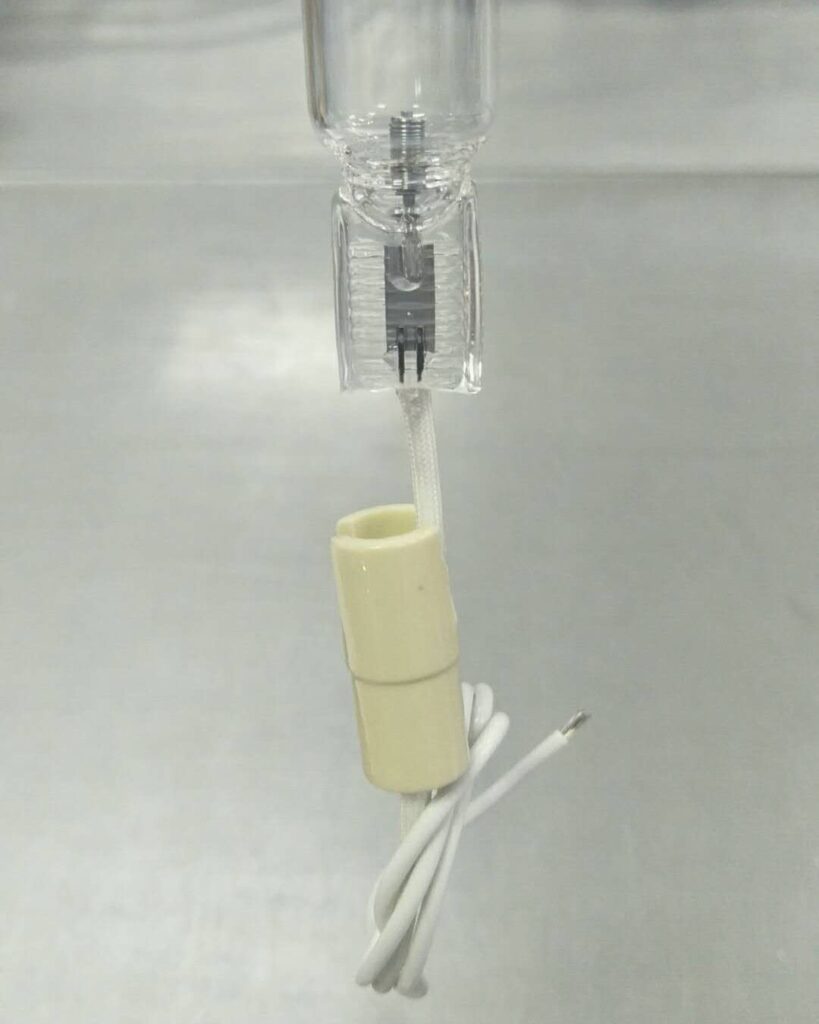
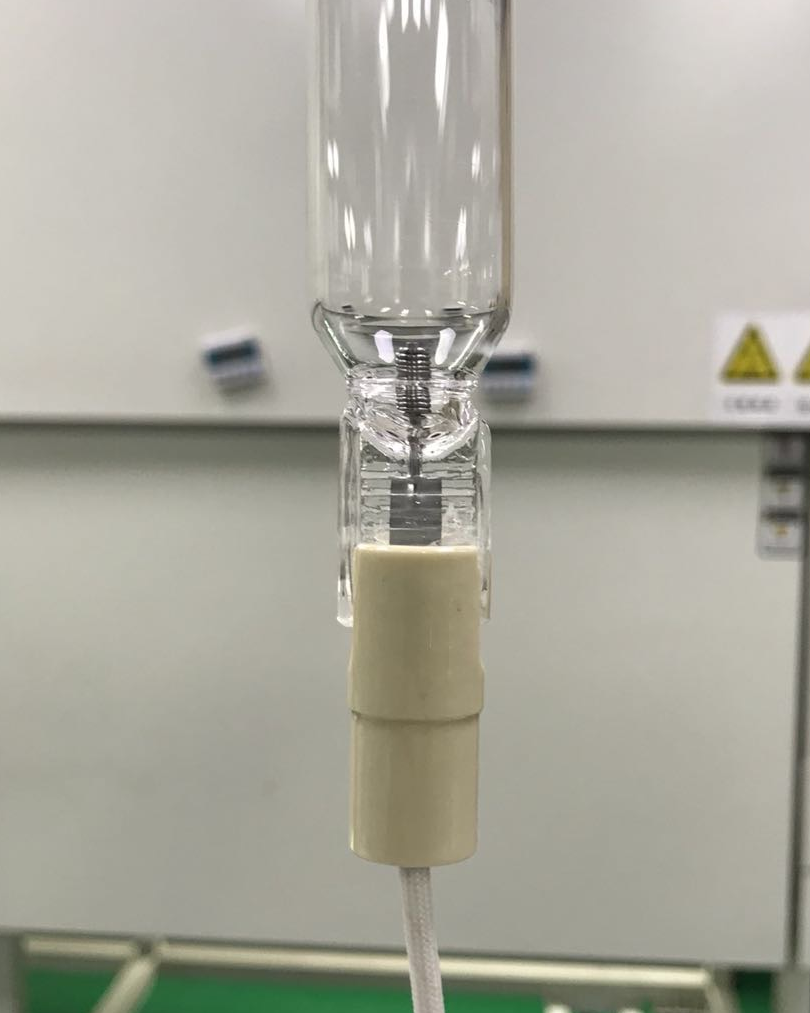
To provide our clients with the best technical support and services, we have invested in equipment capable of conducting varied tests and experiments. With these testing machines, coupled with our full range of electronic power supplies and UV accessories, we deliver unparalleled UV technology solutions to our clients and help resolve various troubleshooting tasks.
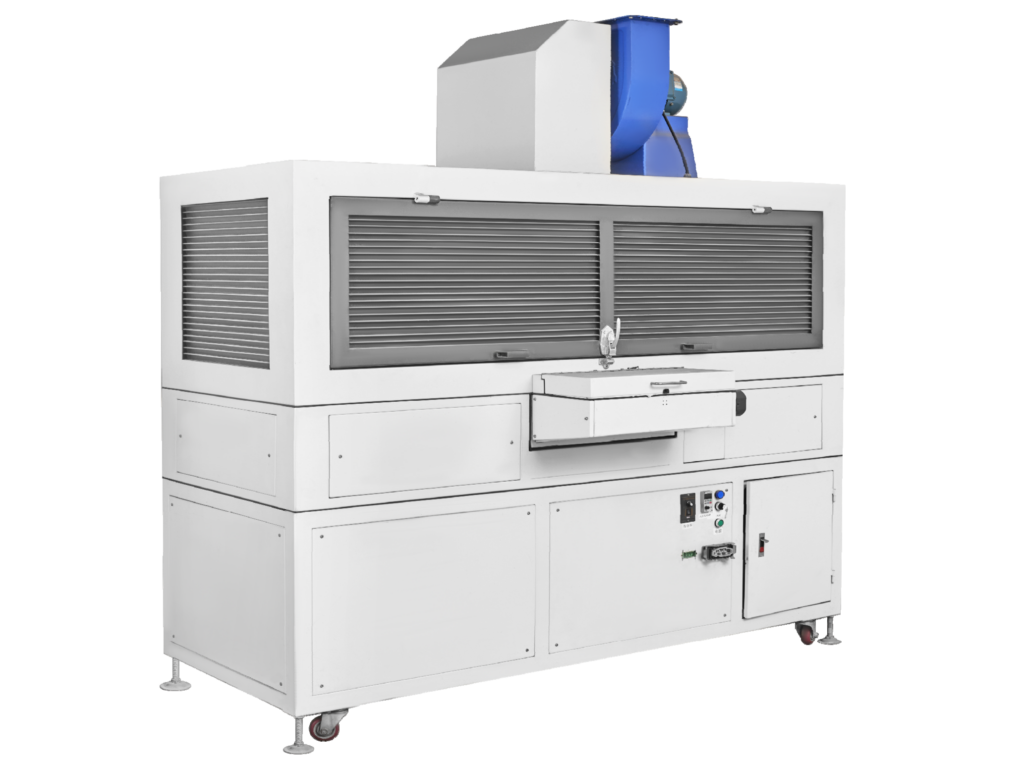
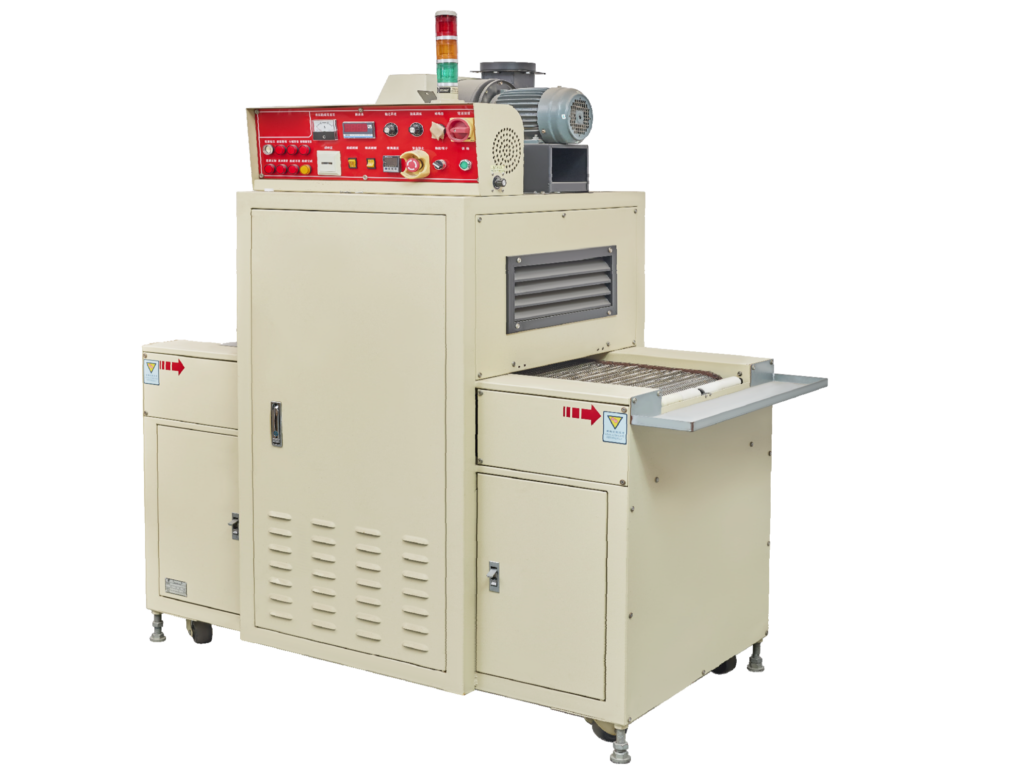
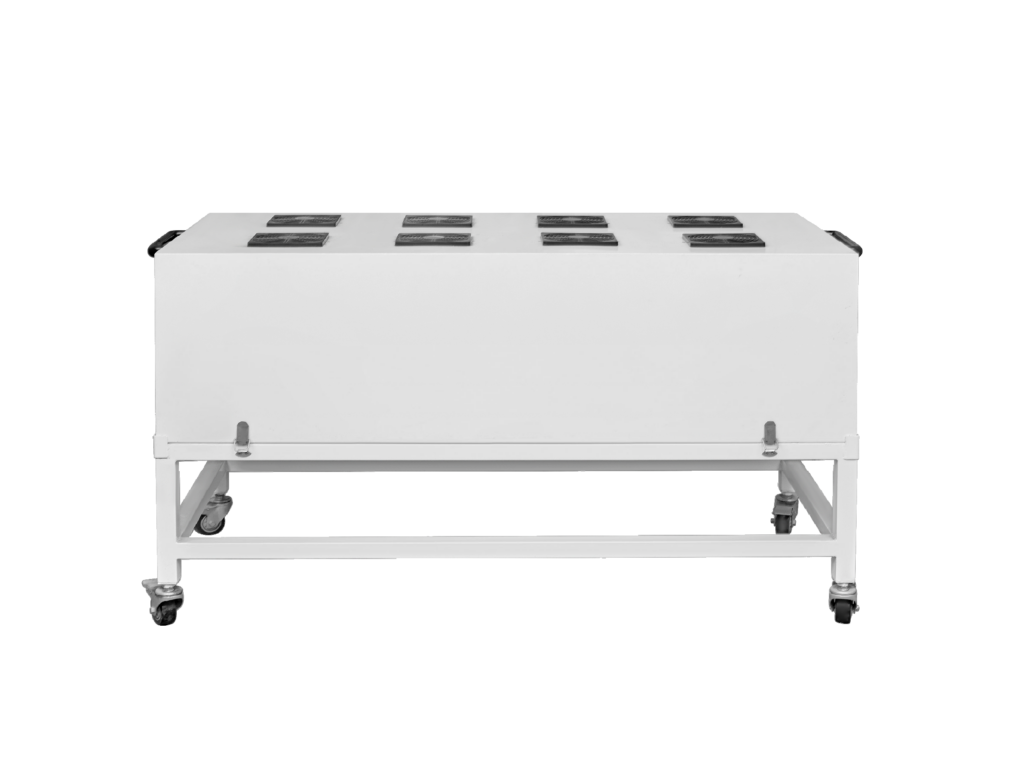
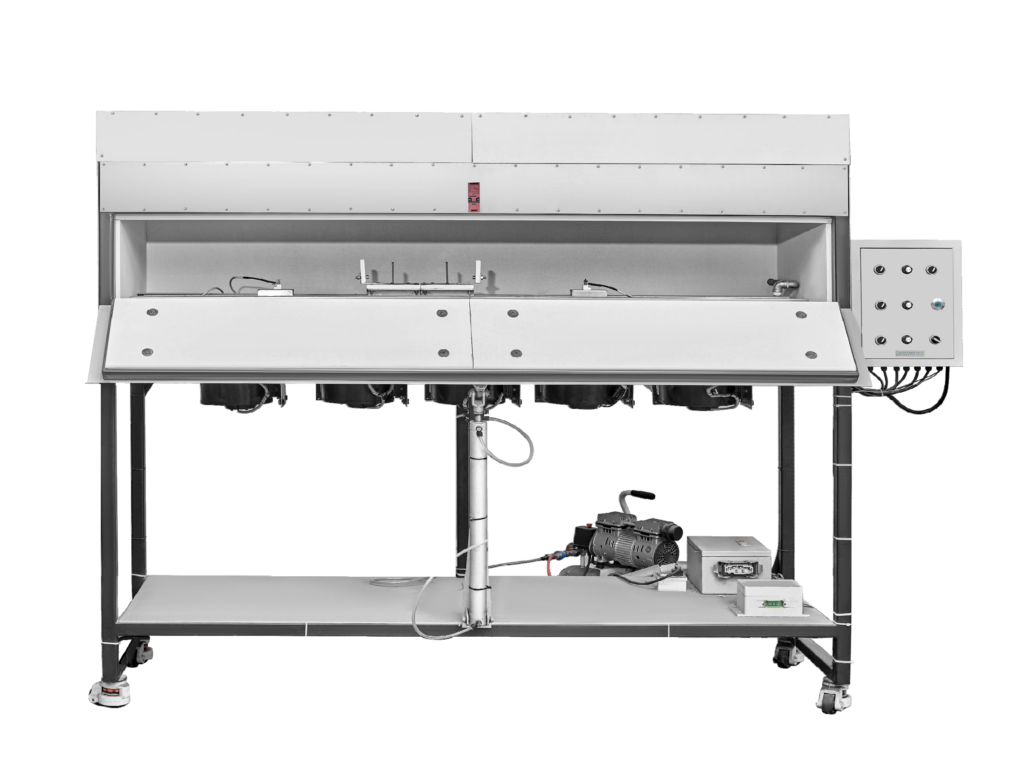
In addition to test equipment, we also have a selection of measuring instruments and service sets to facilitate our testing, development, and troubleshooting tasks.
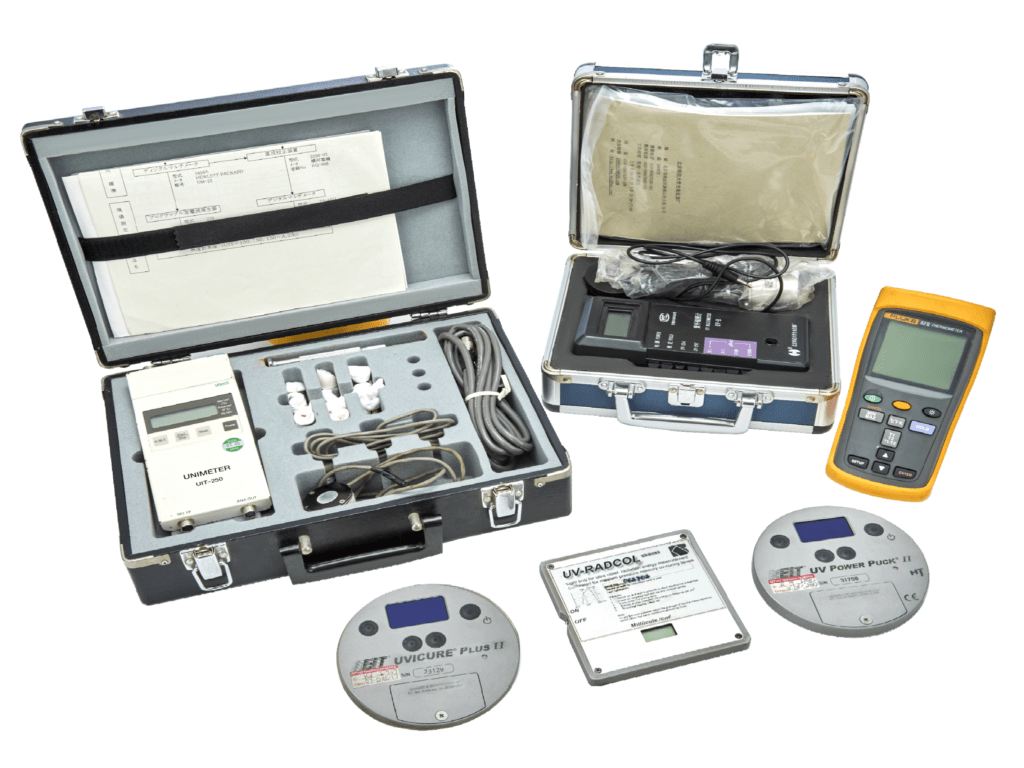
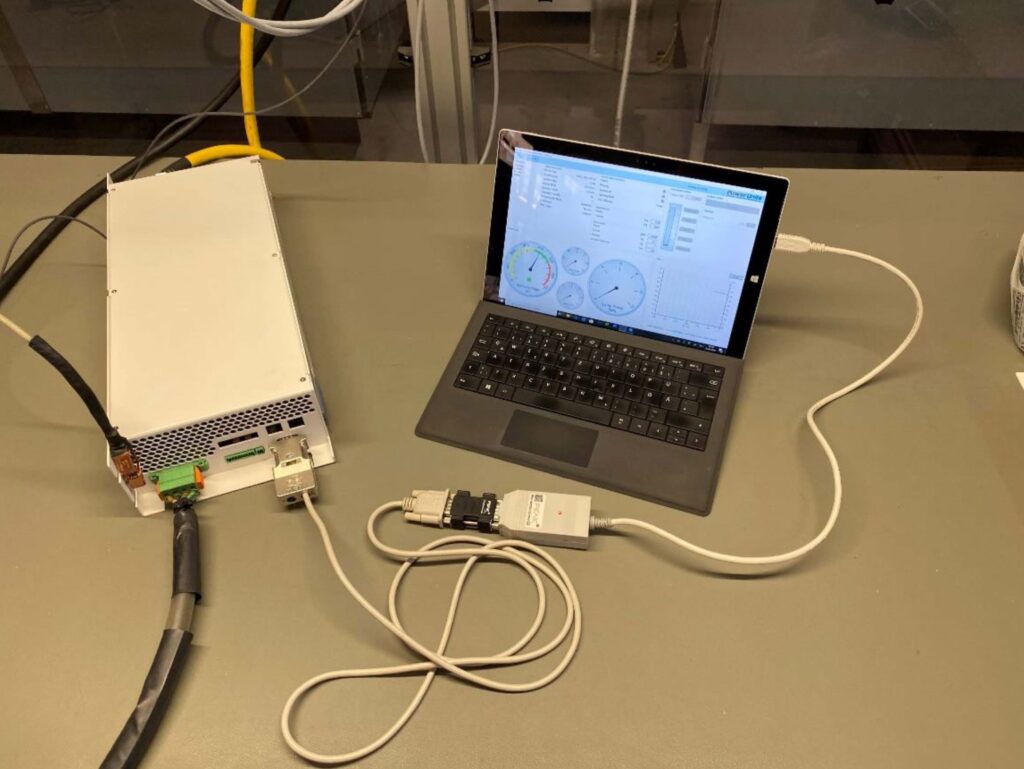
Analyse & develop lamps
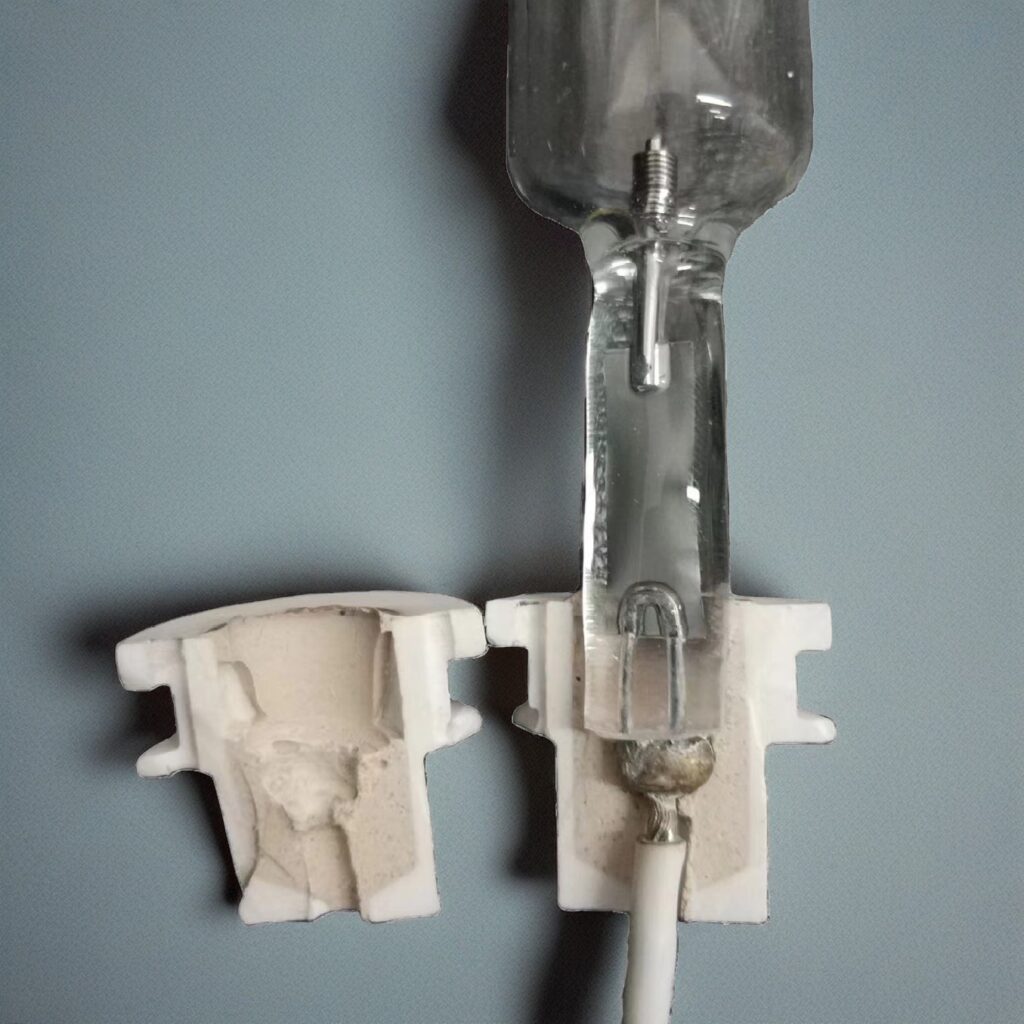
We value our customers’ needs for UV lamps. To ensure that our lamps function seamlessly with our customers’ systems, we carefully test the samples provided by our customers. If customers do not have a working sample, we establish parameters and develop lamps based on their equipment specifications, power supply data, cooling capacity, and UV intensity requirements.
With our comprehensive service offerings, which include a wide range of electronic power supplies, PCAN USB adapters, and the intelligent OPA software (Operation Performance Analyzer), we can capture complete and accurate data for virtually any UV lamps through testing.
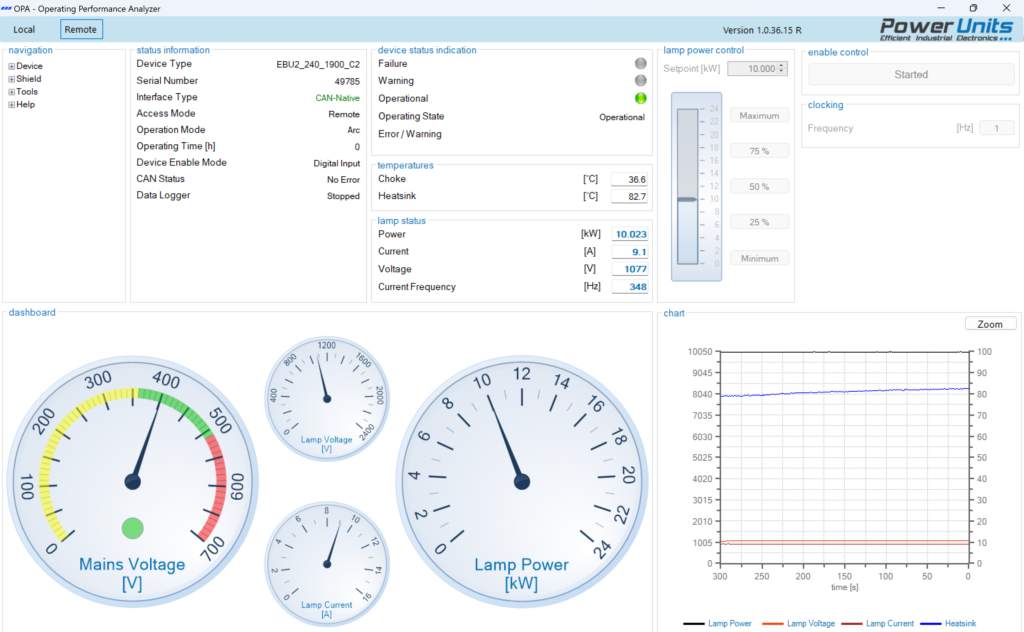
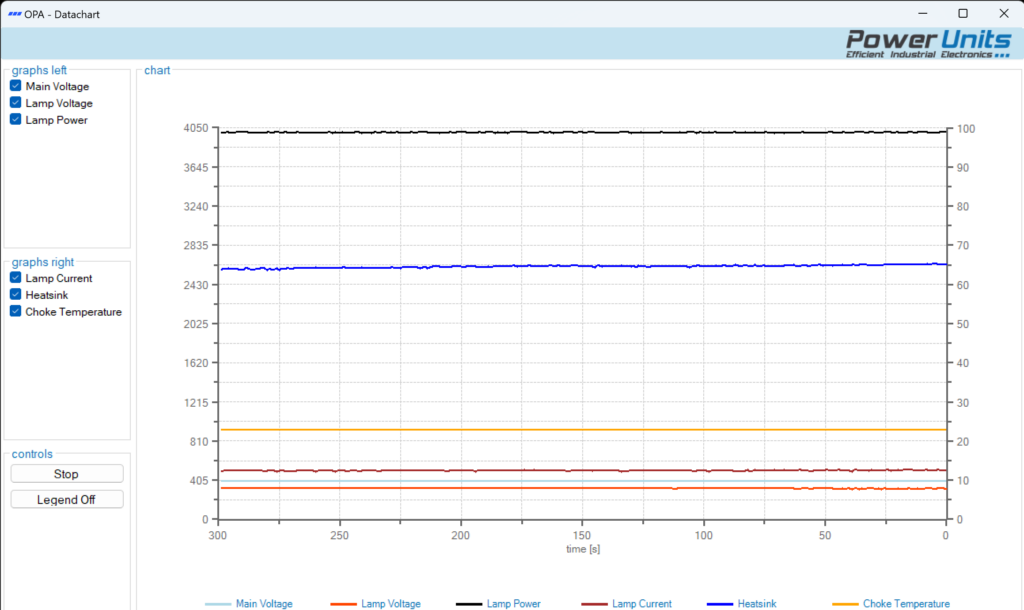
We ensure that the lamp being tested operates at an optimized temperature for a sufficient duration with proper cooling. This guarantees consistently accurate volts and amps.
Afterward, we recalculate and adjust the test values based on the degradation of the lamp sample. Considering the linear power that our clients require and the cooling capability, we select the most suitable diameter of the quartz tube. Consequently, we take pride in developing lamps with closely aligned parameters, even when our clients provide used lamps with unknown data.
Troubleshooting
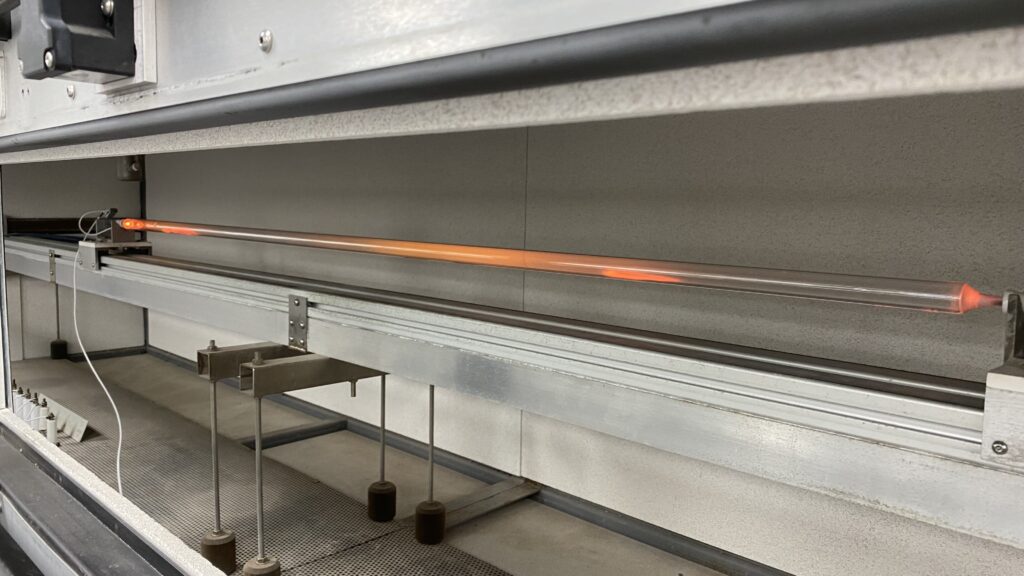
Aside from testing, analysing, and developing lamps, we also offer troubleshooting for various technical and quality issues that our clients may encounter. Our goal is to help solve problems and optimize the performance of our clients’ system.
The localization issue with some specific metal halide iron lamps is complex and challenging. We solve the problem by adjusting the lamp design, along with parameterizing our electronic power supply to successfully tackle this issue.
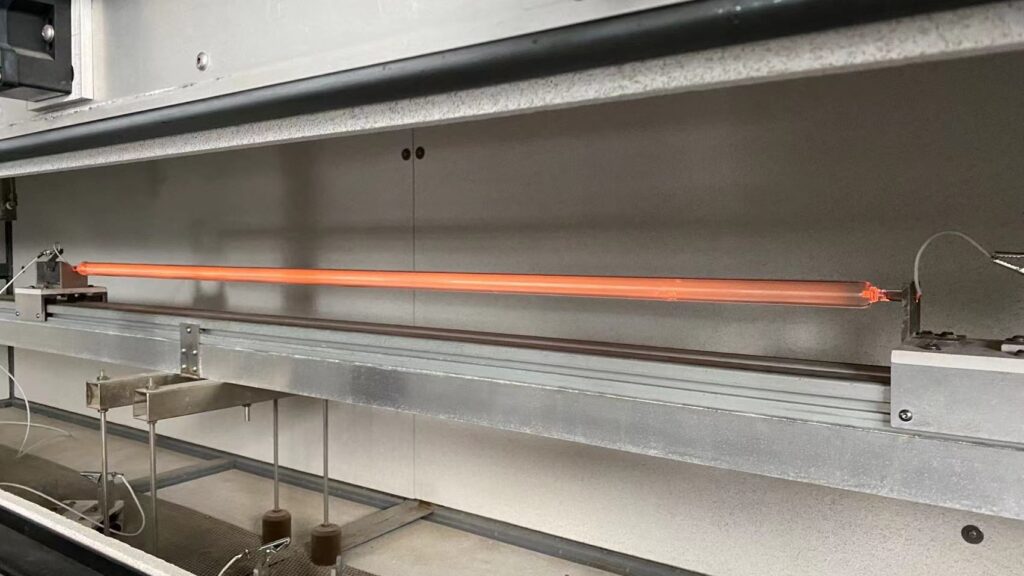
We strive to go above and beyond our clients’ expectations. Here are some of the common technical issues that our clients may encounter with their UV systems.
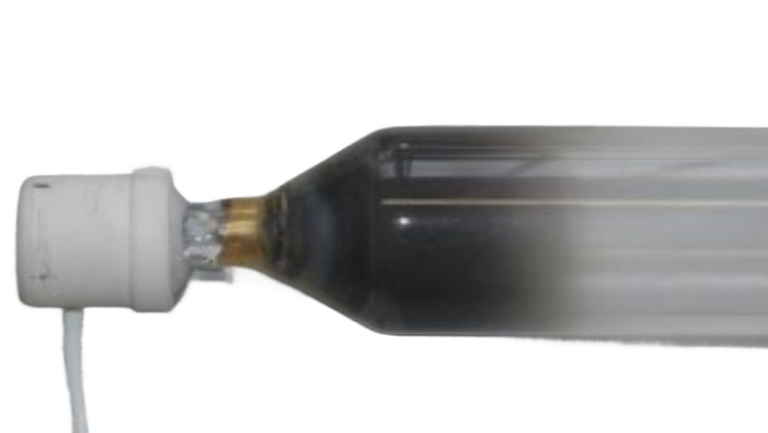
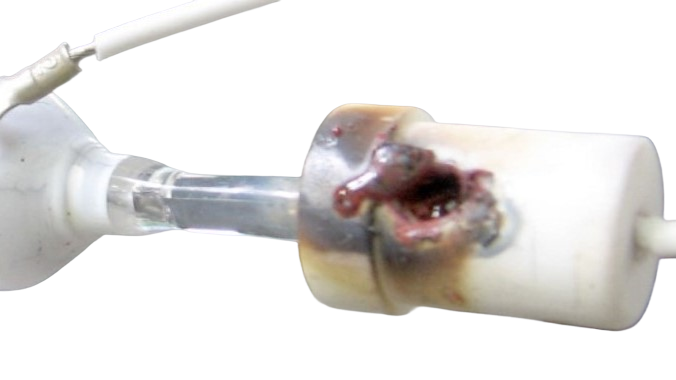
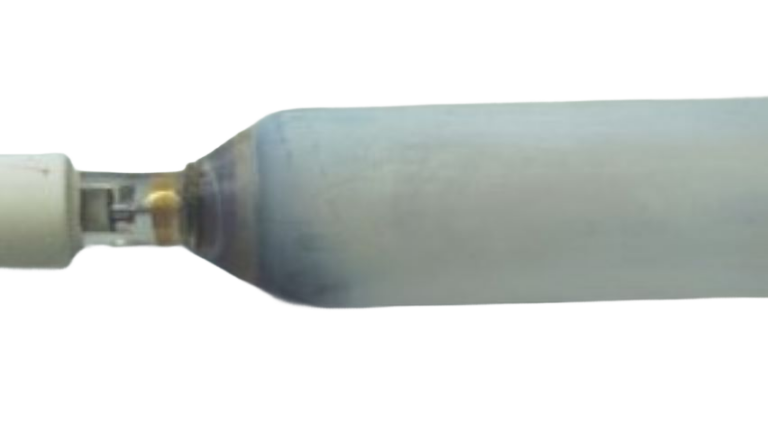
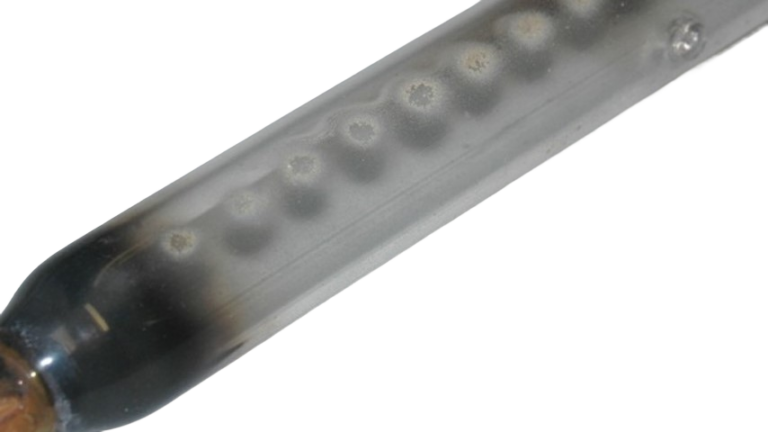
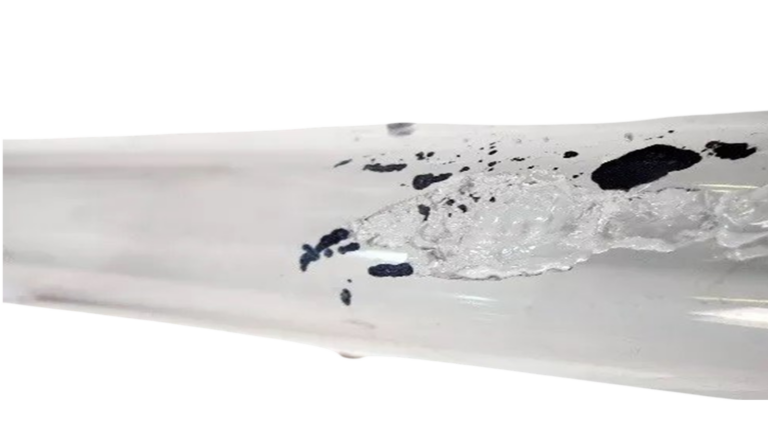
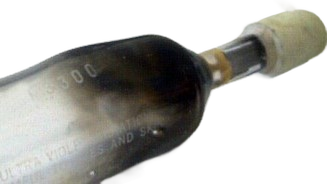
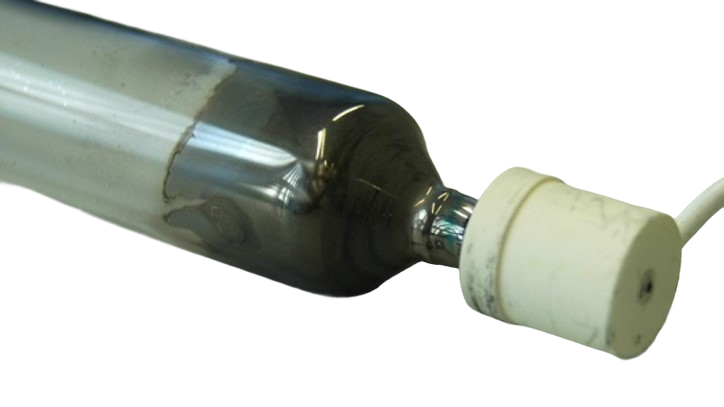
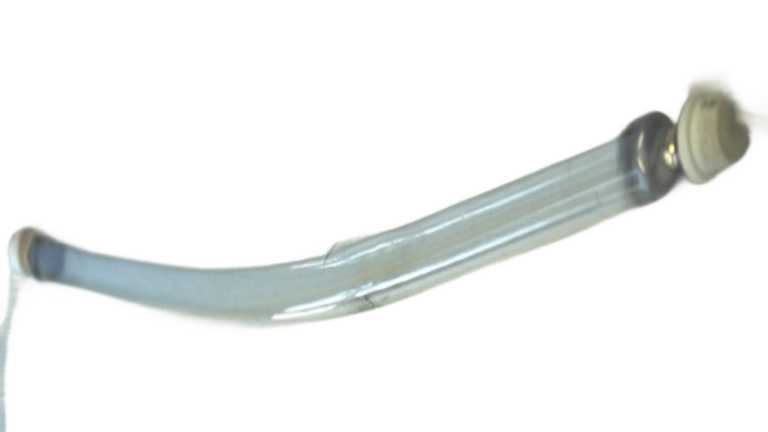
From a technical perspective, the failures mentioned above are, in part, due to the faults of the lamps themselves. Through our investigation, we often find that the problems are more commonly attributed to external or environmental factors. For instance, the lamp tube may deform, or the molybdenum foil may burn due to overheating when cooling is insufficient. Conversely, the ends of a lamp may become blackened with prolonged excessive cooling. Meanwhile, improper handling or external contamination, such as failing to wear gloves during lamp installation or pollutants from ambient air, can lead to the lamps becoming stained with fingerprints, dust, or grease. These external contaminations, when the lamp is operating at high temperatures, can become embedded and burn into the lamp quartz, leading to clouding and devitrification. Our troubleshooting tasks help our clients enhance their understanding of proper lamp handling and system maintenance, thereby preventing similar issues from recurring.
Optimise UV systems
We assist our clients in inspecting, adjusting, and replacing reflectors along with other essential accessories and components to enhance and optimize the performance of their UV systems.
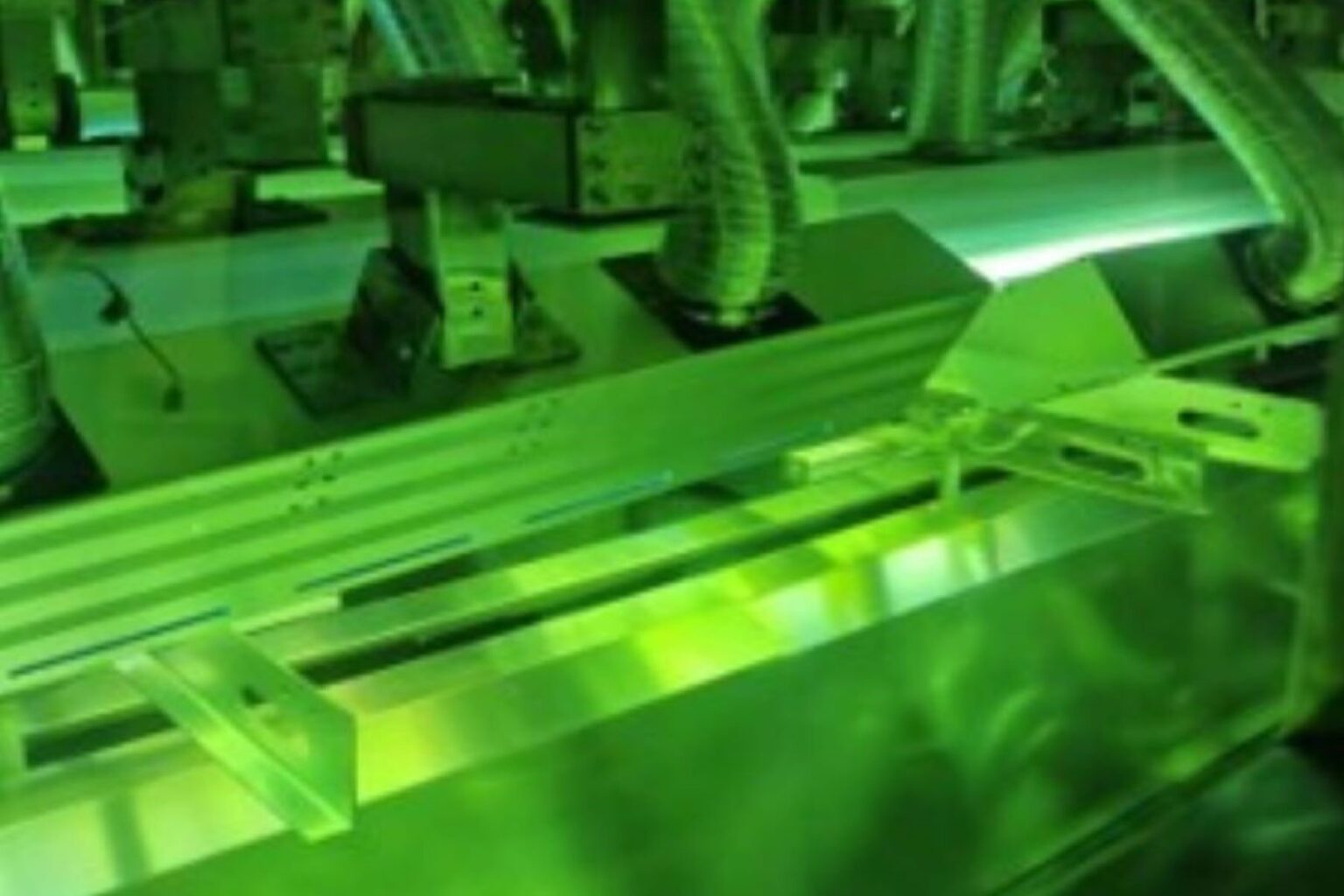
An exceptional UV system maintains the ultraviolet lamp at the optimal temperature, enabling it to achieve its longest possible lifespan. This system also ensures consistent and optimal ultraviolet energy and intensity. Furthermore, the irradiated temperature can be controlled within the ideal range to meet production requirements.
The optimal operating temperature for a UV lamp ranges from 600°C to 900°C. Quartz glass begins to degrade at elevated temperatures, resulting in a significant reduction in energy output and lifespan. Conversely, excessively low temperatures can hinder the complete vaporization of mercury or metal halide, leading to blackening, a shortened lifespan, decreased UV intensity, and ultimately ineffective curing.
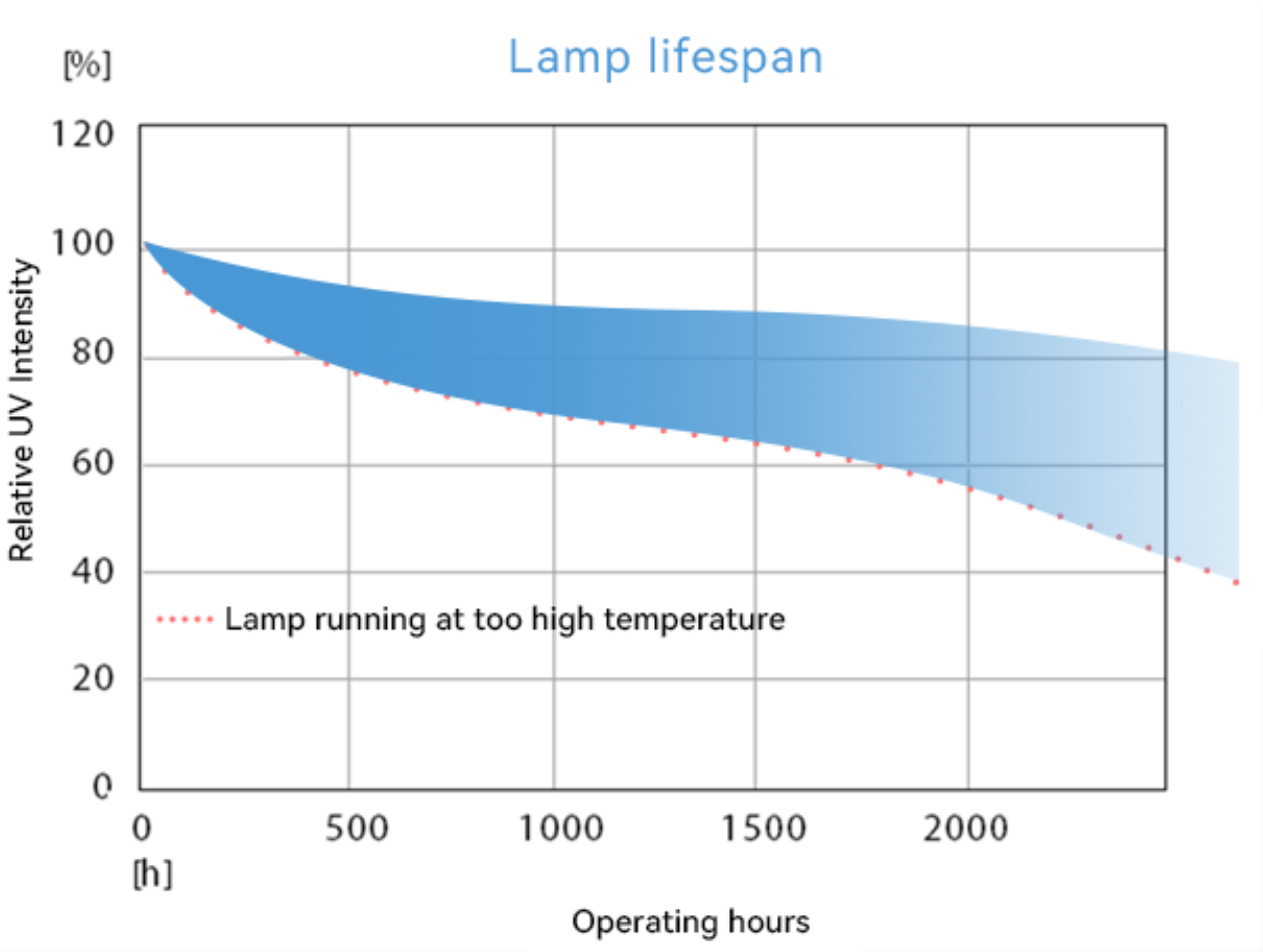
To achieve the longest lifespan for lamps, it is crucial to ensure they operate at an optimal temperature of 700°C. We assist our clients in measuring and regulating the temperature of their lamps, ensuring they achieve optimal performance even when operating at varying power levels.
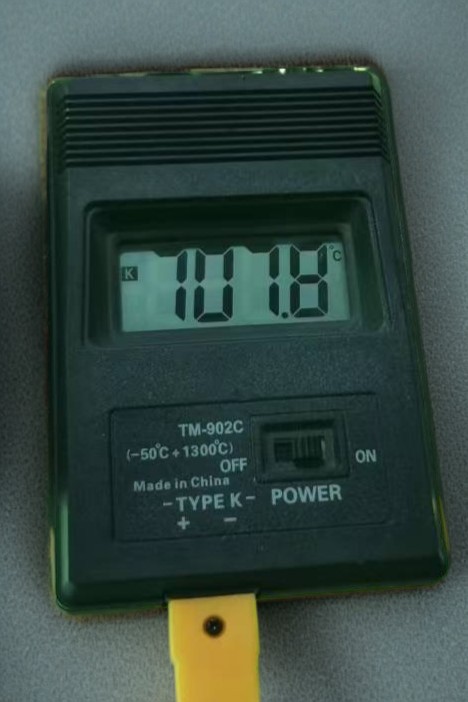
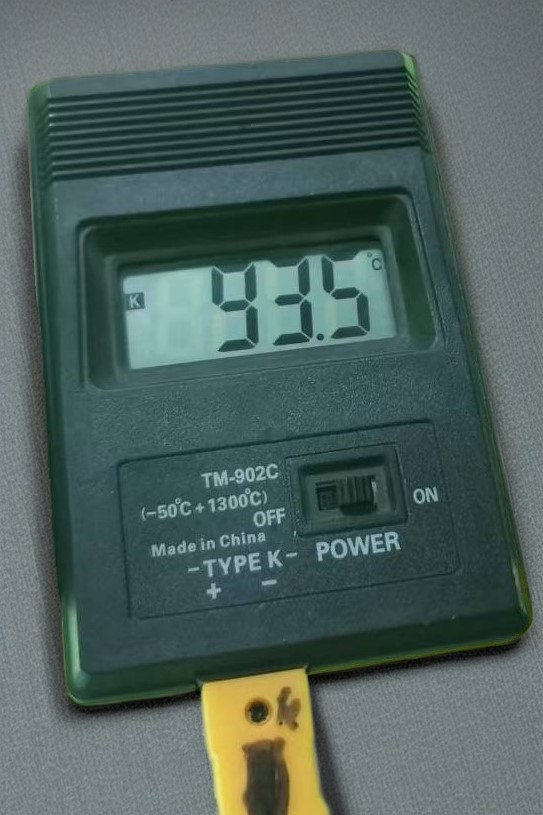
We physically measure the most appropriate surface temperature for the lamp’s operation while simultaneously measuring a reference point for monitoring and control. As shown, when the lamp operates at 707.8°C, the temperature at the reference point measures 93.5°C.
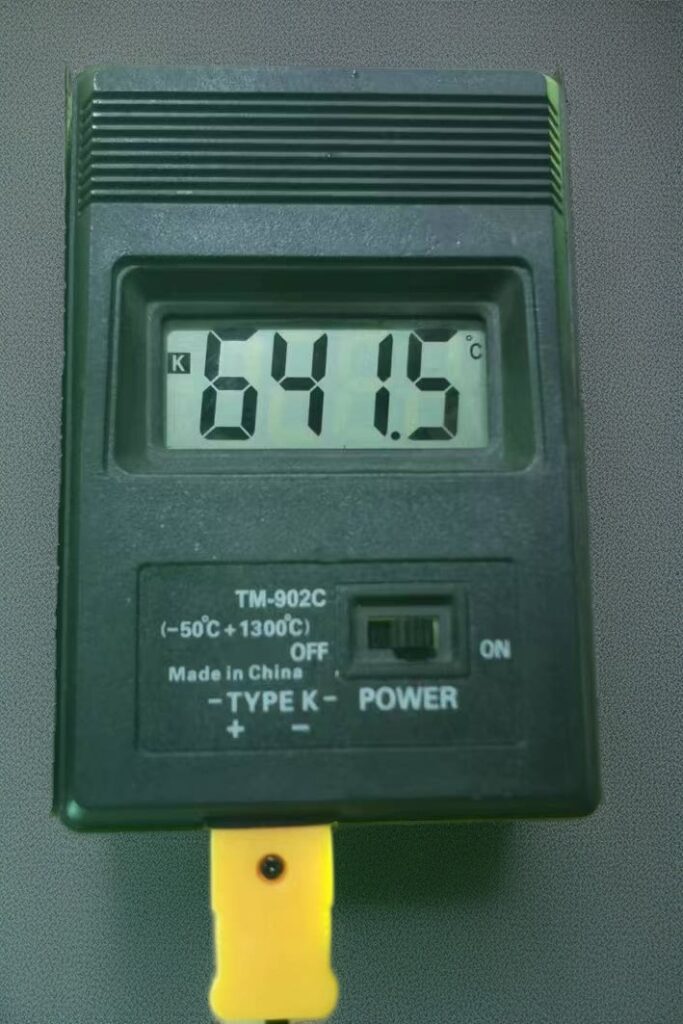
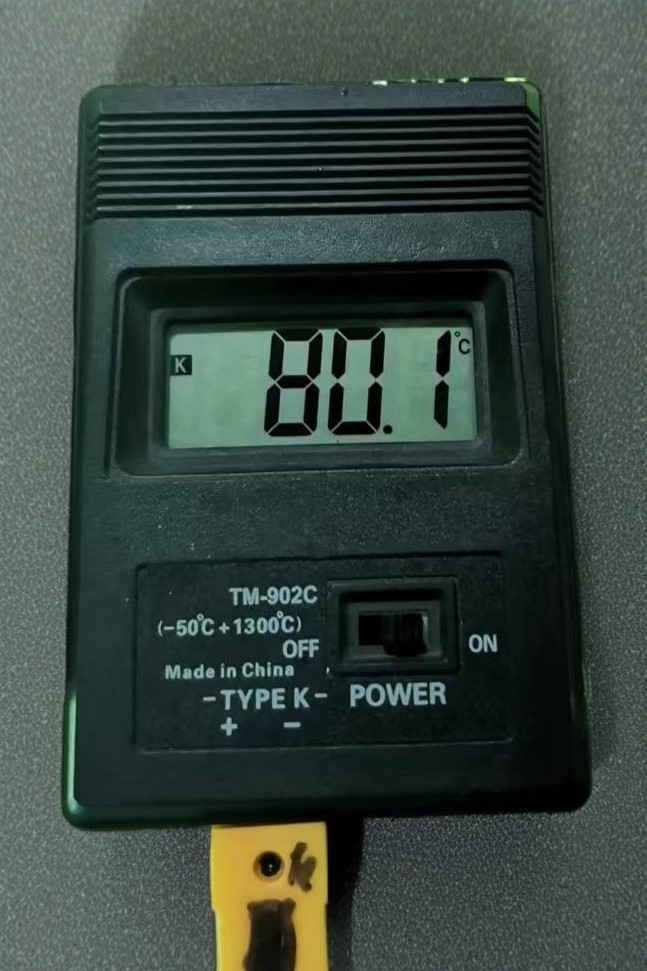
However, when we reduce the lamp power while maintaining the same cooling, the temperatures of the lamp surface and the reference point both drop to 641.5°C and 80.1°C, respectively. This clearly demonstrates the linear relationship among lamp power, temperature, and cooling. To effectively manage and regulate the lamp temperature at the optimal 700°C, using an inverter fan is essential and appears to be an excellent solution.
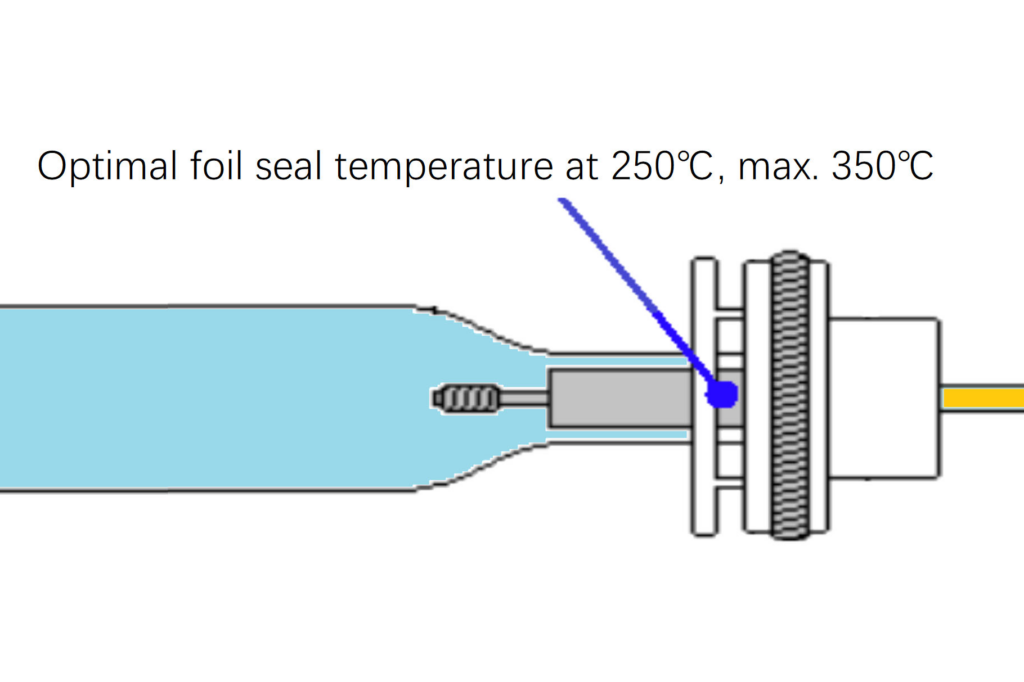
The molybdenum sealing foil oxidizes at high temperatures when exposed to oxygen. Therefore, the higher the temperature, the more readily the foil seal oxidizes, leading to premature failure. Optimizing the lamp’s surface temperature aids in maintaining the foil seal within the desired temperature range.
Based on UV technology and experiments conducted worldwide over the past century, the molybdenum sealing foil is best maintained at 250°C, with a maximum temperature of 350°C. At Anniwan, we take pride in helping our clients optimize their UV systems with the appropriate cooling methods to achieve both optimal lamp surface temperatures and foil seal temperatures.
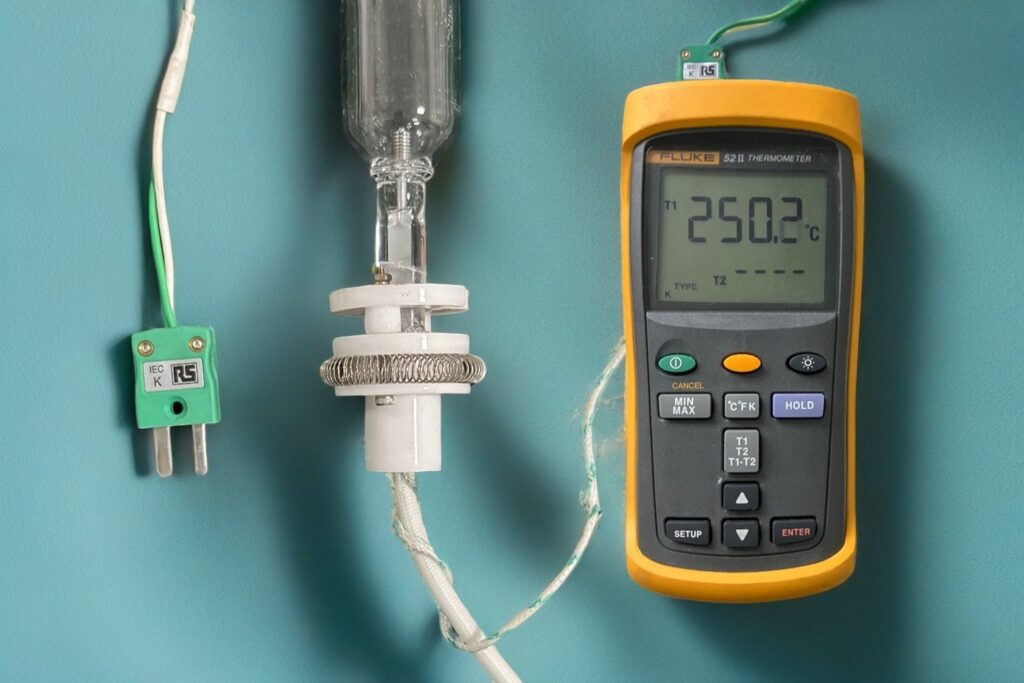
Electronic repairing
In addition to our warranty on the power electronics provided to our clients, we also offer value-added services for repairing damaged electronic devices, even those with expired warranties, using genuine and original electronic components and IC parts from our OEM manufacturers.

Our technically skilled team, with their extensive knowledge of our electronic devices, meticulously measures and cross-checks the circuitry of the 4-layered PCB to identify any damaged electronic components or IC parts.
With a supply of genuine electronic components and IC parts from our esteemed OEM electronic ballast manufacturer, we repair and restore damaged devices, allowing them to continue operating and surpass our clients’ expected lifespan.
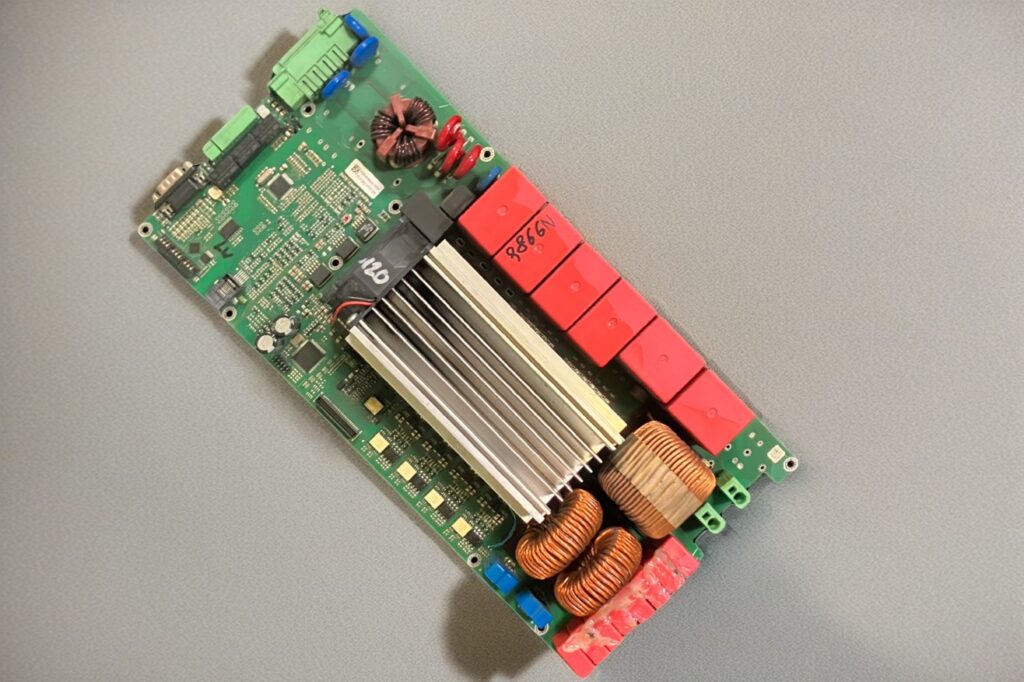
Supply of UV accessories
In addition to offering a variety of UV lamps and a complete selection of electronic ballasts, we also provide a range of UV accessories that are essential for building UV systems and optimizing UV spectral output.
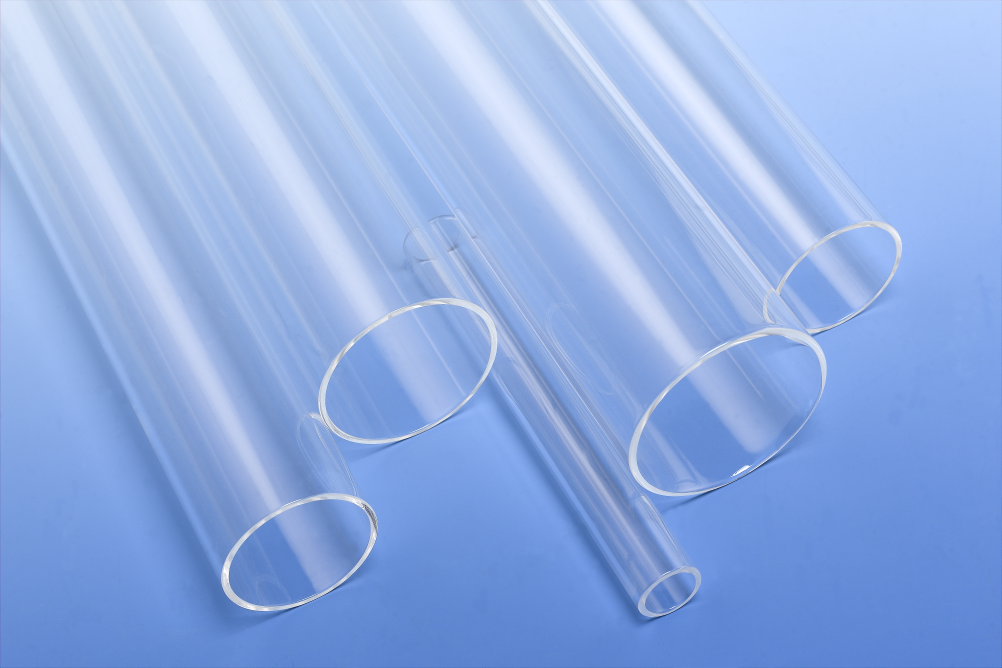
Our extensive range includes a diverse selection of high-purity standard and synthetic quartz tubes meticulously crafted to meet various applications and industry-specific requirements, particularly in the ultraviolet (UV) sector.
Precision-cut and large-sized high-purity quartz plates are available for specific requirements in UV equipment construction and other custom applications.
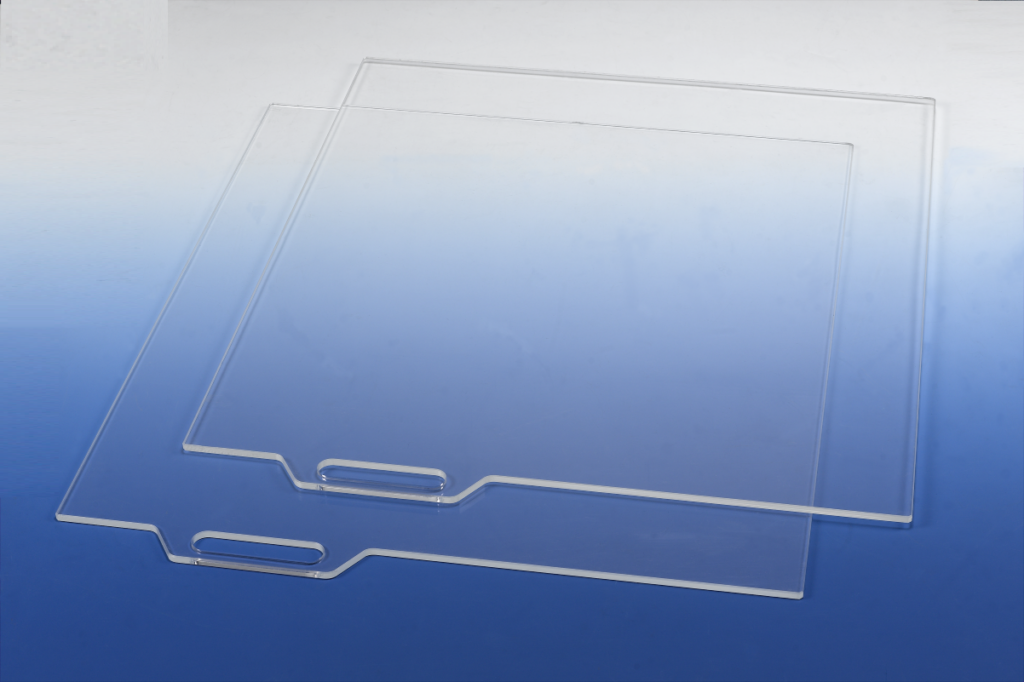
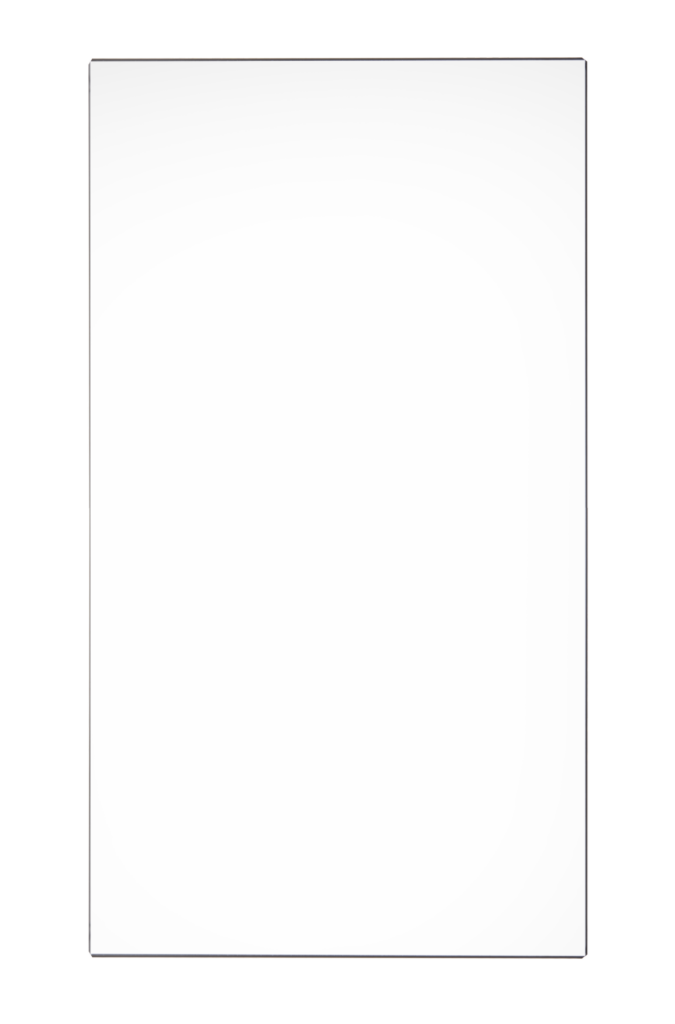
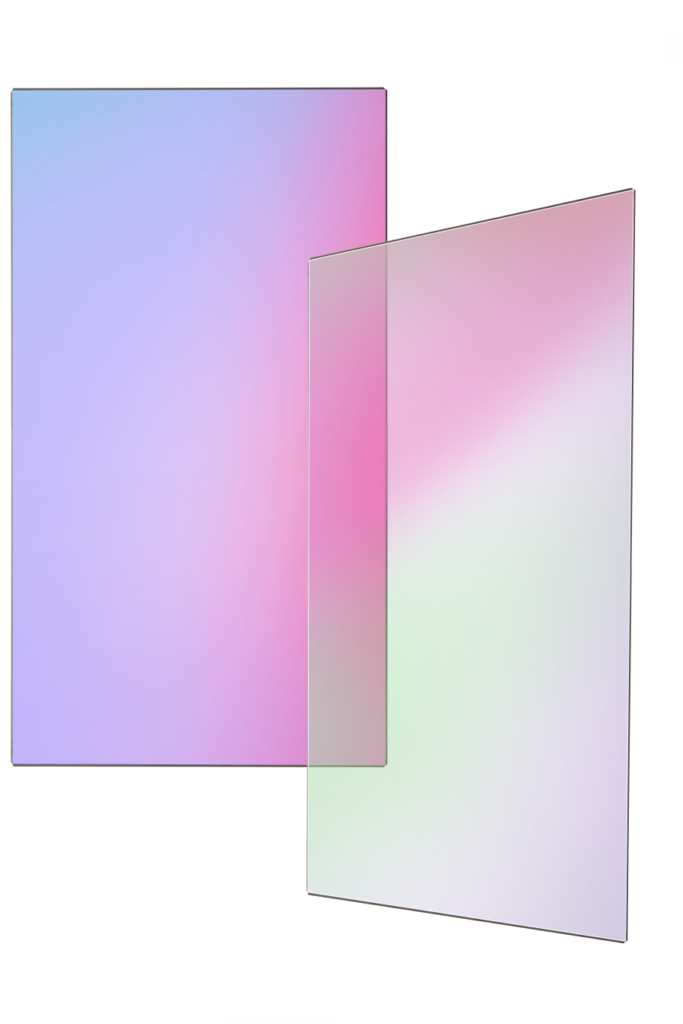
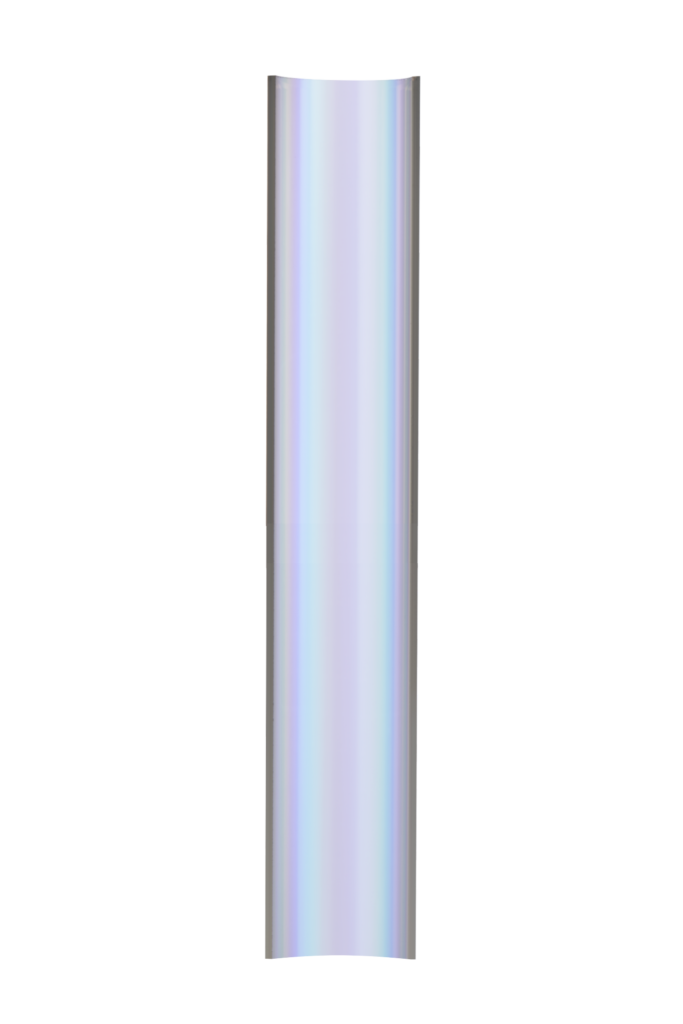
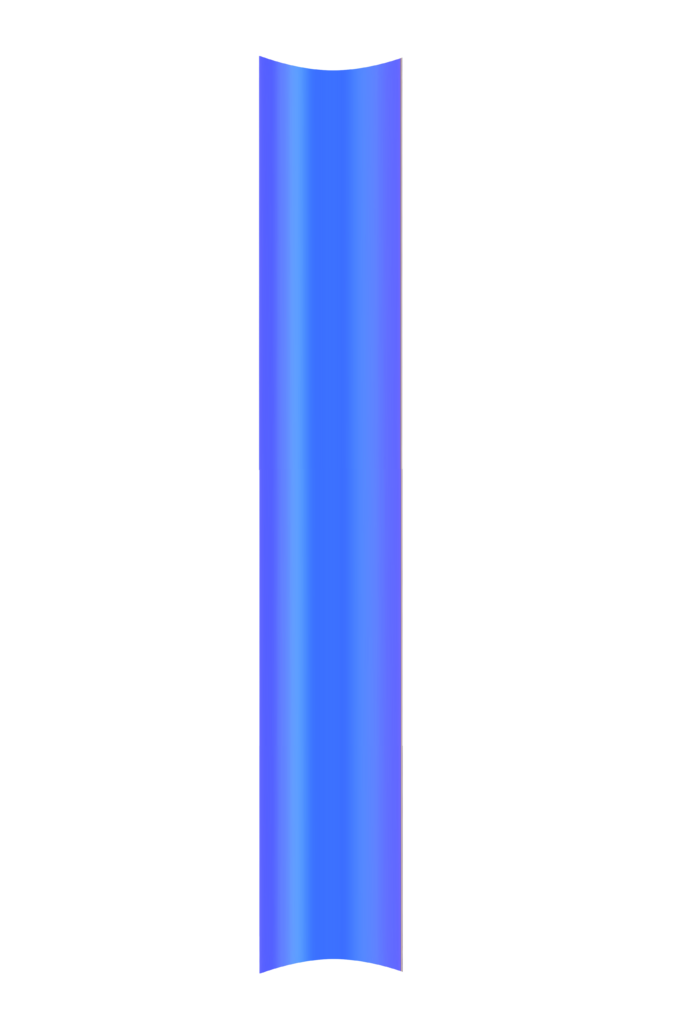
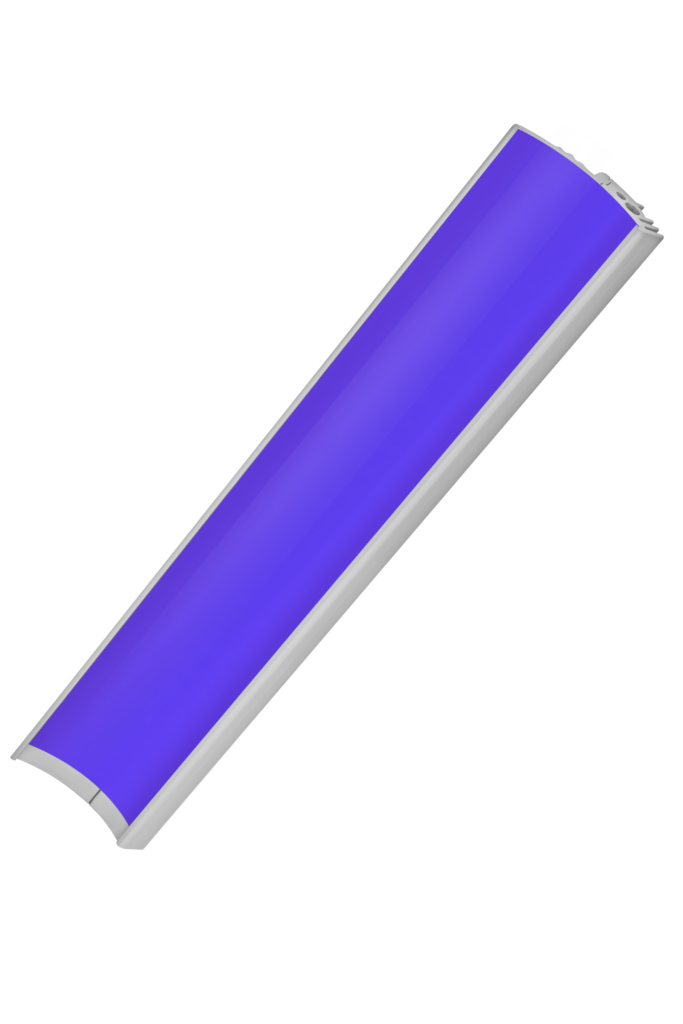
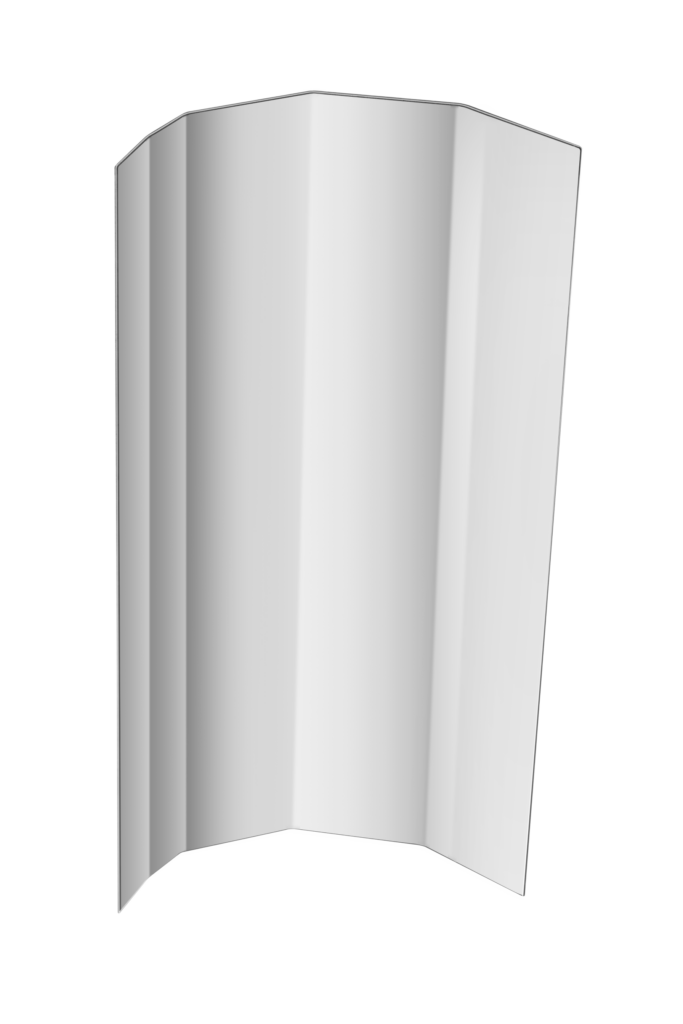
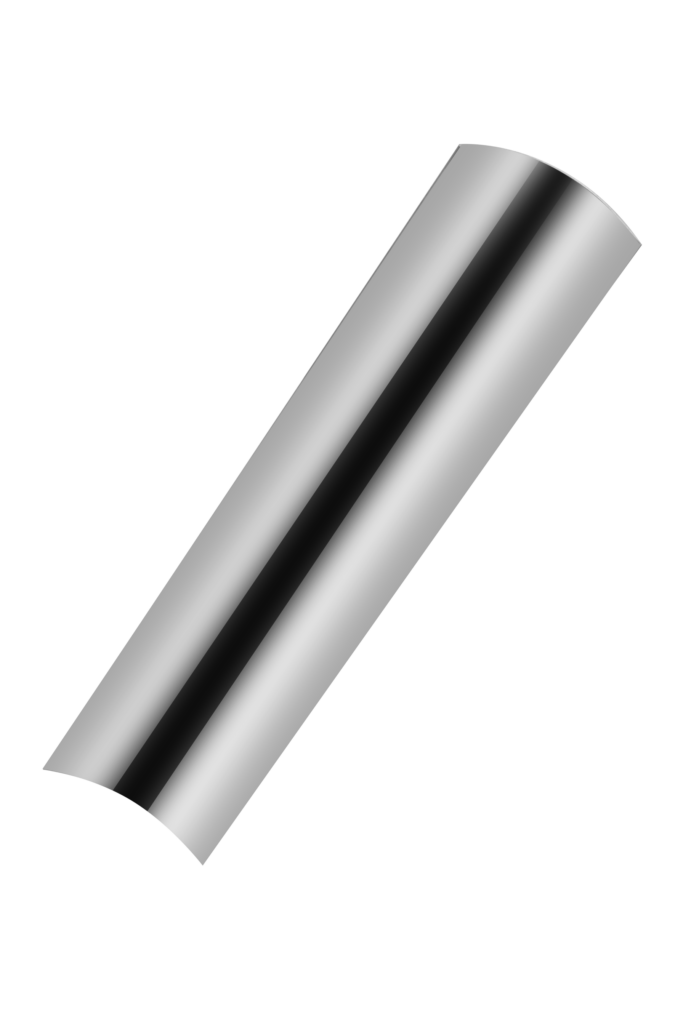
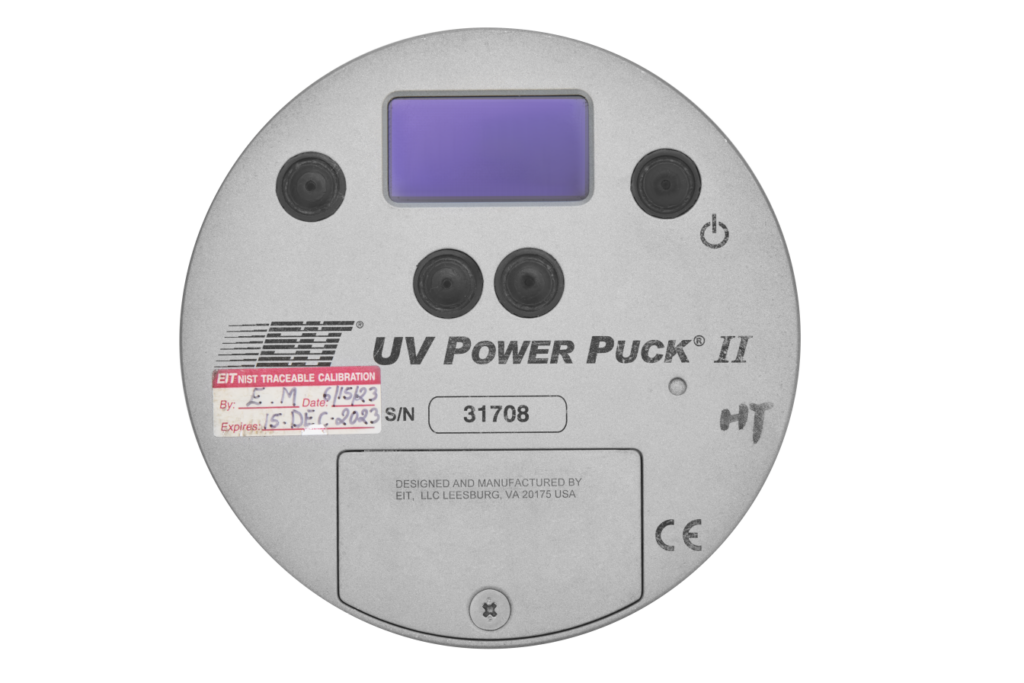
Customer service
Striving to serve our customers and provide the best after-sales and technical services has always been our unwavering pursuit. With the mission to be recognized as the preferred provider of UV technology solutions, we are committed to delivering UV management services and engineering support that are dependable, sustainable, and cost-effective for our clients.
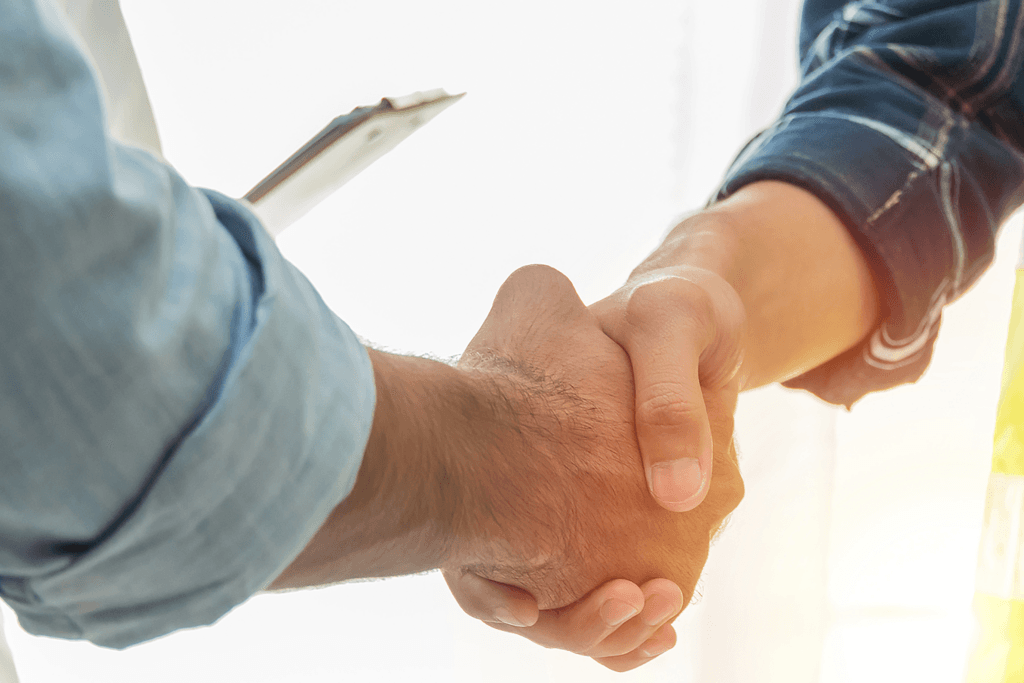
Fueled by a spirit of entrepreneurship, enthusiasm, and determination, we carry out all tasks with the utmost sense of responsibility and accountability.
We don’t merely pledge our commitment; we surpass expectations by diligently and proactively addressing our clients’ technical challenges and bolstering their UV application capabilities to enhance their overall strength and competitive edge.
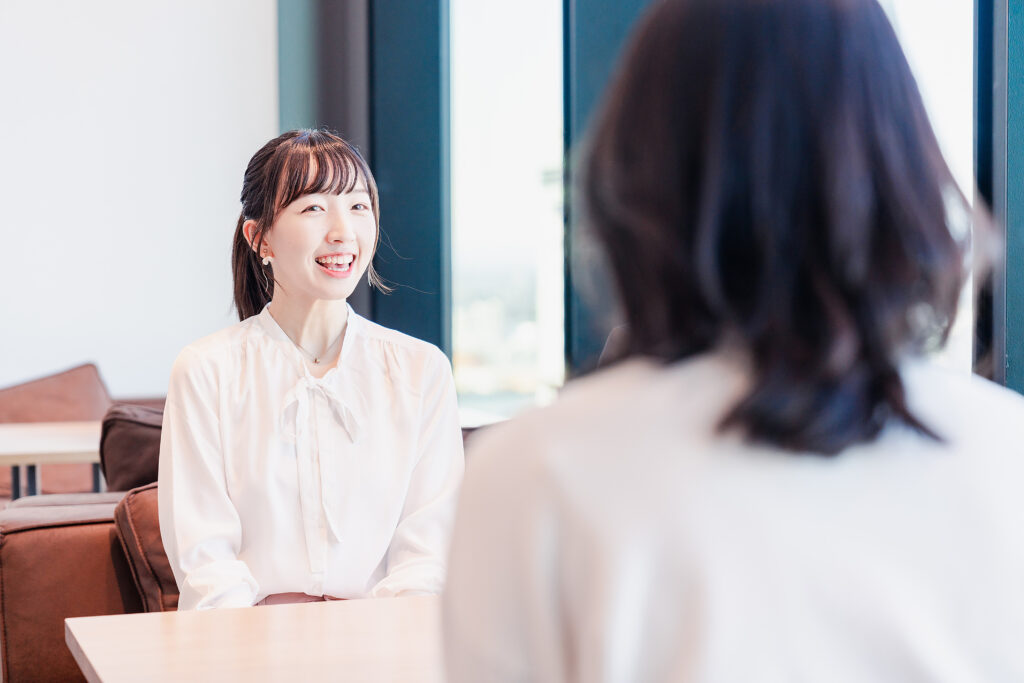
Contact with us
Please reach out to us if you have any questions about our products & services. Our dedicated technical and sales teams will contact you shortly.